Taking the time to perform regular maintenance, such as cleaning and immediate repair of minor issues, will help prevent masonry repairs in the future. While a major project, like rebuilding a wall or extensive repointing, can cost thousands, preventative maintenance can be done for less.
If you’ve noticed cracks or discoloration in your brickwork, or other signs of masonry damage, call a professional right away. Click the Masonry Repair Long Island to know more.
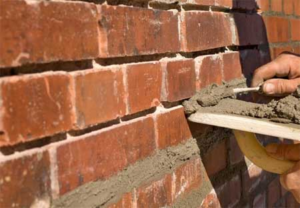
Cracks in brick walls are often the first sign of serious masonry problems and can lead to structural damage in your home or business. Cracks can range from hairline to wide and jagged. Masonry cracks can be repaired but only when the underlying cause is identified and corrected.
In some cases, a simple filler will solve the problem, but in many situations you will need to remove and replace damaged mortar. This is called tuckpointing and involves replacing the existing mortar with fresh mortar to restore the integrity of the structure.
Prior to repairing the cracked areas, you will need to make sure that your safety is a priority by wearing protective equipment such as work gloves and a dust mask. You will also need to clear the affected area of any debris, dust and dirt to ensure proper adhesion of the new mortar. You will then need to mix the new mortar, which is generally a mixture of 3 parts sand and 1 part mortar. This will need to be brushed into the cracked areas, making sure to fill all of the empty joints and to cover any remaining dirt or debris with the new mortar.
Cracks in masonry are normally caused by thermal movement, shrinkage and moisture infiltration. It is important to address these issues quickly before they get worse. Harsh weather conditions like freezing and thawing cycles can further exacerbate existing cracks and moisture infiltration. In addition, structural overloading of the masonry can lead to cracking. To avoid these issues, you should consider having an engineer evaluate the masonry wall to determine the root cause of its failure and recommend appropriate repairs.
Loose Bricks
Brick is a resilient building material, but the natural wear and tear of weather conditions and ground movement can cause bricks to loosen. If left unchecked, loose bricks can become a domino effect that destabilizes the entire structure and poses both aesthetic and safety concerns.
Loose bricks can be repaired by re-mortaring them. This is also known as tuckpointing, and it is a critical step in maintaining the structural integrity of masonry structures. Masonry repair professionals are skilled at assessing the extent of damage, identifying underlying causes, and employing advanced techniques to restore structural integrity.
If you need to replace a loose brick, first remove any surrounding mortar and clean the area thoroughly. Using a mason’s chisel, carefully chip away any remaining mortar from the brick to create a clean opening for the new mortar. Using a brush and water, clean the edges of the opening to ensure that there is no dirt or debris left behind.
Apply a fresh layer of mortar, filling the space to the top and both sides of the old brick. Allow the mortar to set and dry. If the brick is on an incline, support it with a board until it has a chance to set and stabilize.
If you need to tuckpoint a wall, begin by clearing out the existing mortar joints, using a mason’s chisel and hammer for larger gaps or a power grinder with a masonry cutting wheel for smaller gaps. Clean the holes of any lingering dirt or dust, and vacuum or blow away any leftover debris. Moisten the area with a water hose or garden sprayer on a mist setting and keep it damp for at least three days to help the mortar bond with the bricks and cure properly.
Water Damage
Masonry is the method of building with bricks and mortar that creates those gorgeous old buildings you often see in city neighborhoods. While masonry is no longer the primary way in which homes and commercial buildings are constructed, it remains a popular choice and should be carefully maintained to keep its structural integrity intact.
There are many signs that you need to look out for in masonry, including cracks and other structural problems. Often, these signs will be visible on the surface of the brick, but they may also show up in walls or other building structures. If you are seeing any of these signs, call a professional masonry repair contractor immediately to have the problem fixed.
One of the most common signs that masonry needs to be repaired is water damage. This can occur in many different ways, from leaks to moisture seepage through the brick. The best way to prevent this is to have a professional inspect your masonry regularly, especially after periods of heavy rain. A skilled mason can spot potential problems before they turn into major issues that require repairs or even replacement.
Another common sign of water damage in masonry is staining. This is almost always the result of water, and can be a serious issue for buildings. Staining is not only unsightly, but it can also lead to structural damage and cause the masonry structure to shift or collapse.
If you notice that your masonry is stained, a professional mason can replace the affected bricks and clean the area to prevent further issues. In some cases, the staining can be caused by a lack of proper caulking, which should be addressed immediately. If the staining is a result of moisture, the professional mason will find and fix the source of the water to prevent it from occurring again.
Expansion Joints
Expansion joints are gaps or spaces built into brick walls to allow the natural expansion and contraction of building materials. These gaps are important in the longevity and structural integrity of brick walls. Without them, the wall would crack and eventually collapse over time. Expansion joints are often overlooked by homeowners, but they are an important part of the overall foundation of your home.
Masonry repair professionals can restore damaged or faulty expansion joints to their original condition, extending the lifespan of your home’s exterior. Having your expansion joints repaired correctly can also minimize tripping hazards.
Ideally, expansion joints should be located at both ends of the brick structure, and in any areas that change direction. This will allow for the expansion and contraction of all materials in the structure, preventing damage to the masonry walls.
The size of the gap in the expansion joint will depend on the length and height of the wall, as well as the expected temperature changes. It is recommended that these gaps be no larger than 12mm.
The type of joint filler you use in your expansion joints will also determine the durability of the joint. Strip seals are flexible neoprene membranes that adhere to the joint walls and provide outward pressure on the wall to prevent water ingress. However, these types of seals can tear or disjoin if incompressible debris settles on top.
If you want a longer-lasting and more resistant option, consider using a silicone expansion joint sealant. Silicone is flexible, resilient, and bonds well to masonry and metal. It is especially effective in areas with wide temperature fluctuations and withstands traffic better than other polyurethane sealants.
Shelf Angles
Shelf angles are long L-shaped pieces of metal that are inserted behind rows of bricks to help distribute the weight of the building. When they’re corroded, it can create holes in the wall and leave gaps between bricks. Masonry experts can replace the spalled bricks and repair the corroded shelf angle to restore the integrity of the wall.
In addition to their structural role in supporting masonry veneers that cannot be directly supported by foundations or interstorey slabs, they can also act as thermal bridges. This is because they provide a direct pathway for heat to transfer between the backup wall and the masonry, bypassing the insulation layer. In order to mitigate this issue, it is recommended that shelf angles are connected to the structural framing using a structural thermal break.
When the structural thermal breaks are connected to both the steel shelf angles and the concrete structural framing, they can help improve both the load-bearing capabilities of the connections as well as their thermal performance. It is also important that the structural thermal breaks are properly sized to accommodate short-term elastic deformations of the concrete superstructure and long-term chemical shrinkage and expansion of the clay brick veneers.
It is also recommended that the thermal breaks be connected to both the steel shelf angles and the backup wall using a through-bolt connection. This ensures that the thermal breaks can effectively support the load at the attachment connection while interrupting thermal bridging. In addition, the use of stainless steel bolts can also improve the thermal performance of the connections by lowering their coefficient of thermal conductivity (CTC).